General
Fasteners are manufactured in a wide range of materials from common steel to titanium, plastic and other exotic materials. Many materials are further separated into different grades to describe specific alloy mixtures, hardening processes, etc. In addition, some materials are available with a variety of coatings or plating to enhance the corrosion resistance, or appearance of the fastener.
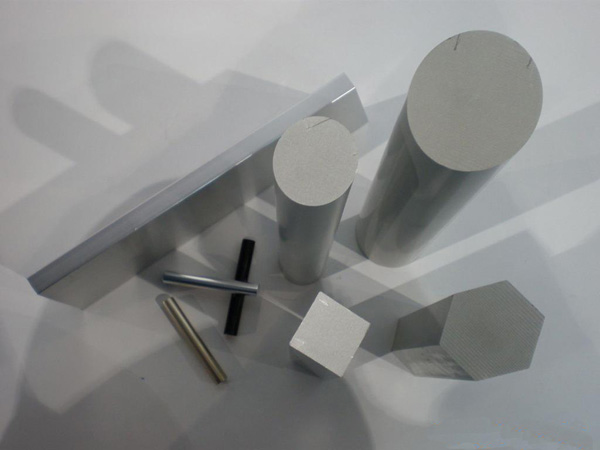
Fastener material can be important when choosing a fastener due to differences between materials in strength, brittleness, corrosion resistance, galvanic corrosion properties, and of course cost.
When replacing fasteners, it is generally best to match what you are replacing. For example, replacing a bolt with a stronger one is not always safe. Harder bolts tend to be more brittle and may fail in specific applications. Also some equipment is designed so that the bolts will fail before more expensive or critical items are damaged. In some environments such as salt water galvanic corrosion must also be considered if changing fastener materials
Materials
Low carbon Steels -
The high ductility of these grades gives them excellent formability.
Low carbon steels produced to minimum strength requirements form the basis of non-alloyed structural steels.
And are widely
used in applications where strength is required beyond that obtained from simple mild steels, without significant loss of formability or weldability.
Properties: Combination of good strength and ductility. Available in a variety of yield and tensile strengths to suit specific applications.
Typical applications: Automotive and agricultural wheels, pulley wheels, construction sections and supports.
Medium to high carbon steels-
Medium carbon steels may be used for some applications in the "as rolled" condition. Both medium and high carbon steels may be hardened and tempered to increase strength and hardness.
Typical applications: Garden tools, chain side plates, load washers, transmission plates, ice skate blades, circular saws and machetes.
Free-cutting Steels -
Free-cutting steels are ideal where high degrees of machining are required as they increase machining speeds and reduce tool wear.
Lead is added to low carbon re-sulphurised steel to further enhance the free-machining performance. Tata Steel also provides a free-cutting steel without lead, that offers improved free machining performance.
Typical applications: Keys, contact boards and other parts requiring rapid metal removal.
18.8 Stainless Steel - includes several alloys:
302: ASTM A276 Type 302; A167 Gr.2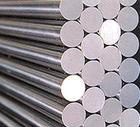
XM7: 302HQ for cold heading screws
303: ASTM A582 Type 303; A320 Gr. B8F; A194 Gr. 8F
304: ASTM A193A Gr. B8; A320 Gr. B8; A194 Gr. 8
Contain approximately 18% chromium, 8% nickel, are non-magnetic and hardenable by cold working; a tensile strength range of 80-200,000 psi; good corrosion resistance. Used in food, drug and chemical equipment; bearing plates; heat exchanger tubes; pumps; valves.
316 Stainless Steel: ASTM A193 Gr.B8M; A276 Type 316; A320 Gr. B8M. Contains 18% chromium, 8% nickel and 2-3% molybdenum. Better corrosion resistance than other grades, particularly in chlorides; 80-170,000 psi tensile strength; non-magnetic and hardenable by cold working. Widely used in textile, paper mills, chemical plants, and marine applications
304L and 316L: Low carbon grades. Minimize carbide precipitation during welding and exposure to high temperatures.
17-4PH: 15 - 17% chromium, 3 - 5% nickel, 3 - 5% copper
410 Stainless Steel: ASTM A276 Type 410; A193 Gr. B6. Magnetic and less corrosion resistant than other stainless alloys but hardenable.
Inconel: 70% nickel, 12% chromium, 2% iron. Good strength and corrosion resistance at high temperatures. Used in aerospace, food processing industry and refineries.
Monel 400: ASTM B164 Class A. Approximately 65% nickel, 32% copper. Nearly non-magnetic, 82,000psi min. tensile strength; strengthened by cold working. Heat (to 800 degrees F) and corrosion resistance. Used in chemical, electrical and saltwater marine applications as well as offshore engineering, salt production, and hydrocarbon processing.
Monel 405: ASTM B164 Class B. For machining.
Monel 500: "K" Monel. Approximately 65% nickel, 30% copper, 3% aluminum. Age hardenable for improved strength and hardness. Pumps and marine applications.
Hastelloy C-276: 60% nickel, 16% molybdenum, 15% chromium. Resists corrosion in acidic environments. High strength at extremely high temperatures. Typical applications include equipment components in chemical and petrochemical organic chloride processes, pulp and paper digesters and bleach areas, flue gas desulfurization (FGD) scrubbers, pharmaceutical and food processing equipment.
Brass: 65% copper, 35% zinc. Good strength, corrosion resistance and workability.
Silicon Bronze 651 & 655: ASTM B98 Alloy 651 or Alloy 655; B99 Alloy 651 or Alloy 655. 95-97% copper, 2-3% silicon, 1% manganese. More corrosion resistant and stronger than brass. Used in electrical circuitry in switchgears, etc., as well as valves and process control equipment.
Aluminum Bronze 614: ASTM B150 Alloy 614. 89% copper, 7% aluminum, 2% iron.
Titanium: Very high strength-to-weight ratio, good corrosion resistance and high temperature durability. Excellent aircraft and aerospace material.
Aluminum 2024: ASTM B221 Alloy 2024 -T4; B211 Alloy 2024-T4. 93% aluminum, 4% copper. Good combination of strength, corrosion resistance, light weight and economy. Optimum properties when heat-treated. Widely used in aircraft.
Aluminum 6061: Standard alloy for 录" and larger nuts. Specially made bolts can be made from this alloy.
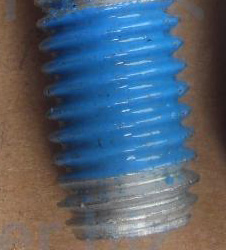
Coatings
Zinc Plating - Many steel fasteners are electro-plated with zinc for better corrosion resistance. Fasteners that have been zinc plated have a shiny silver or golden appearance referred to as clear or yellow zinc respectively. They are fairly corrosion resistant but will rust if the coating is destroyed or if exposed to a marine environment.
Hot Dip Galvanizing - Galvanizing is another coating involving the application of a layer of zinc. Hot dipped galvanizing puts the thickest possible coating on the metal resulting in superior corrosion resistance. Due to the thickness of the coating hot dipped galvanized bolts are not compatible with other nuts. Galvanized nuts are tapped slightly larger than other nuts to accommodate this coating. Hot dipped galvanized fasteners are frequently seen in coastal environments and in pressure treated lumber where the chemicals in the lumber may corrode other fasteners.
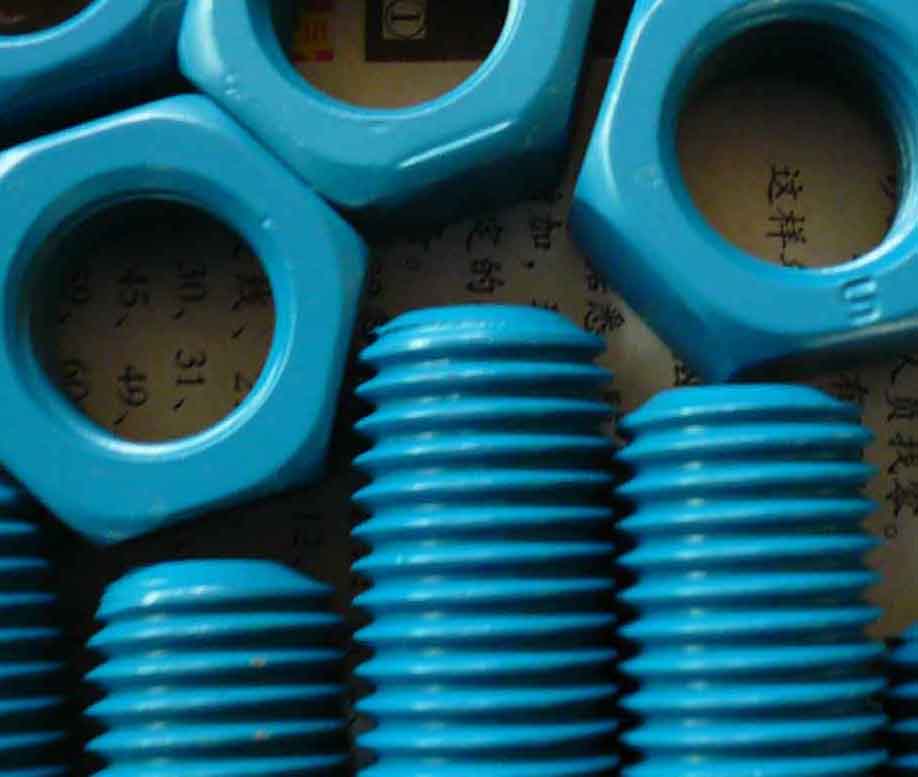
Chrome - Chrome is used in plating fasteners for its appearance. It provides similar corrosion resistance to zinc plating. The main drawback of chrome is the extremely high cost. If more corrosion resistance is required stainless steel may be chrome plated, preventing any corrosion should the chrome be penetrated.